How to Deliver Measured Business Operation Outcomes
Process Optimization: Doing More with Less
Process and asset optimization is top of mind for most operations driven by increased inflationary pressures, constricted budgets and stringent environmental regulations. Whether your goals include increased capacity, decreased off-spec quality, improved yield or reduced energy usage, learn how you can unlock the full potential of your existing assets, process and people.
Needs We’re Seeing from our Clients
If you are directly responsible for delivering measured business operation outcomes, whether you’re a plant, operations or production manager, process engineer or someone supporting continuous improvement initiatives, here’s what you can expect:
- Throughput: Lack of production capacity or constraints hinder the production or extraction of goods in an efficient and effective manner
- Yield: The lack of optimization in manufacturing processes results in unmet performance targets, excessive waste, and resource usage, leading to reduced output, productivity, and efficiency.
- Quality Control: Inconsistent and variable quality product output yielding increased returns and customer dissatisfaction
- Energy Reduction: The higher than desired energy consumption negatively impacts efficiency, sustainability, and specific productivity/output.
If an organization’s business driver changes, they need to change the way they optimize their processes.
How Organizations Can Meet Those Needs
Advanced Process Control (APC) solutions go beyond just offering services for new equipment; they provide a pathway to maximize the potential of current assets, aligning with the industry's growing need to achieve more with less.
APC is a layer of intelligent automation applied to existing control systems. It consists of process modeling expertise and technologies designed to continuously evaluate both current and predicted operational data and make immediate control adjustments to reduce in-process variability and improve overall performance.
An APC solution is commonly connected to the regulatory control via OPC or other industry standard communications methods. The APC is continuously monitoring and adjusting control variables to reduce process variability. It's your very best operator 24/7/365.
One of the ways to achieve APC is through model predictive control (MPC). MPC technologies, such as Rockwell Automation FactoryTalk® Analytics™ Pavilion8®, are designed to understand the limitations of a process, continuously evaluate current and predicted operational data to calculate and make optimal control adjustments. Inclusion of neural networks is used to make predictions based on input data and can be trained to recognize patterns and predict future system behavior.
Common Challenges When Starting this Journey
When implementing a new application or solution for advanced control, we've heard similar pain points or challenges from organizations that slowed or stalled progress and adoption in the past.
These include:
- No real expectations set
- No clear ROI / gains
- Wrong selection of the areas to be optimized
- Lack of user’s staff involvement before the project (and consequently no buy-in)
- The benefits degrading over time
Here’s how we do it differently.
Our ValueFirst® Methodology
Let’s walk through how our ValueFirst Methodology looks in action.
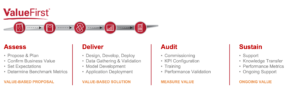
The process starts early with alignment; We help set expectations for a project that are determined together with the user before the project begins - the verifiable results are based on the benefit analysis before the start of the project.
We develop with the user a list of technical and financial goals. The points are continuously checked after the application's implementation to give the user an overview of the services provided and current results (for example, ROI).
As the project is running, users receive regular status reports and for every project, we set numerous performance benchmarks to determine whether the required performance is maintained in every implementation phase. This enables our team to fix any problems before they have any impact on the application.
How APC/MPC Drives Lasting Benefits
- Reduce Variability: Optimize your operations efficiency and accuracy for real time decision making
- Achieve “Plant Obedience”: Adhere to desired operating conditions and respond precisely to control inputs
- Manage the Process within Constraints: Increase visibility to real-time insights
- Achieve Uplift: Operate closer to specifications and performance limits while maintaining safety margins
Eliminate the need to expand and incur the additional capital expenditure, aka greenfield operations.
With the right approach and through our proven ValueFirst® Methodology, process and asset optimization can be achieved by organizations without the need for costly capital expansions. By leveraging advanced process control solutions like model predictive control, companies can unlock the full potential of their assets and drive measurable operation outcomes. Maximize the potential of production systems and workforce with prescriptive analytics and autonomous control to achieve greater throughput and yields. By continuously handling moment-by-moment details, AI services enable organizations to concentrate their expertise on the bigger picture. Meanwhile, MPC and other tools autonomously guide the process toward the set targets.