Recognizing that digital transformation would be essential to building a more scalable and resilient operation, the client partnered with Rockwell Automation and Kalypso to implement a tailored Manufacturing Execution System (MES) extending FactoryTalk®PharmaSuite® well beyond its standard capabilities. By focusing on real-time tracking, streamlined workflows and data integrity we helped reduce waste, increase throughput and ensure patient safety across the globe. The resilience of the system and our continued work together has enabled the operation to scale continuously for over a decade, spanning multiple global locations.
The Impact of a Tailored Implementation
Handling Complex Media Requirements
Working closely with the engineering teams, Kalypso extended Rockwell PharmaSuite® MES well beyond its standard functionality. This included building advanced features to manage thousands of individual media recipes—each mapped to specific test cards—and creating a “container” approach that enabled the system to handle up to 64 sub-orders for every single order from SAP. By digitizing batch records, operators and quality managers gained real-time guidance on temperature thresholds, time-out-of-refrigeration limits and ingredient genealogy.
Automating Key Production Processes
Kalypso helped integrate in-house developed, automated filling equipment. The MES provides machine-readable instructions, tracks every process parameter and receives data back from the equipment to maintain an end-to-end digital thread. This allows for faster scaling and increased throughput, ensuring that even high-volume production meets strict compliance standards.
Real-Time Visibility & Alerts
Teams monitor every stage of production with automated alerts that flag potential hang-time expirations or temperature excursions. For example, if a media bag is nearing its 13-hour hang-time limit, operators and quality teams receive immediate notifications—enabling quick decisions that prevent material loss and lengthy downtime.
Global Rollouts & Continued Expansion
What began in the Saint Louis, MO facility has been successfully scaled across multiple sites, including expansions in Lyon, Craponne, La Balme-les-Grottes and Grenoble, France, and Durham, NC. The MES’s scalability and flexible design accommodate future growth without disruptive system overhauls. Over a decade of incremental improvements demonstrates how a tailored, people-first approach to MES deployment can create both immediate and long-term value.
Business Results
With the new MES in place, production scaled to meet a fivefold increase in demand without compromising quality. Digitizing batch tracking and reducing manual interventions dramatically cut scrap costs, while ensuring an impeccable audit track record—essential in an FDA-regulated environment.
More than just a technology shift, the MES solution and our approach to delivering it has empowered engineers, quality managers and operators to focus on innovation, efficiency and continuous improvement.
Lessons Learned
-
Involve All Stakeholders Early — Engaging operators, quality teams, supply chain staff and leadership from the start ensured that the MES solution addressed real operational needs rather than theoretical pain points.
-
Design for Flexibility — Building a system that could scale across multiple sites and accommodate future automation avoided repeated, costly overhauls and minimized disruptions as demand evolved.
-
Prioritize Real-Time Monitoring — Automated alerts and dashboards drove immediate, data-driven decisions that reduced scrap and mitigated time-sensitive risks, such as media expiration.
-
Invest in Change Management — Providing user-friendly interfaces and hands-on training increased operator adoption and empowered teams to move from manual processes to higher-value activities.
-
Focus on Compliance from Day One — Thorough traceability and validated batch records were embedded into the system design, keeping the manufacturer audit-ready and compliant with FDA regulations at all times.
Partnering with Kalypso created a resilient and agile production environment that saves time, reduces risk and ultimately enhances patient health worldwide with faster, more reliable diagnostic solutions.
Ready to enhance operations and ensure compliance?
Thought Leader
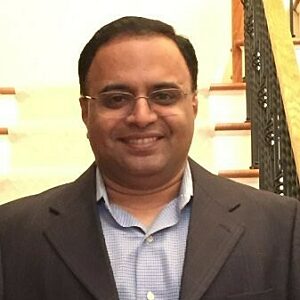