In addition to the complexities of combining separate river/coastal methodologies, there were also concerns around an issue that many companies experience, regardless of size… silos. Departments and practices are spun up to address immediate issues, and if they work well enough, then they can be left to their own devices. The “right hand” doesn’t know what the “left hand” is doing simply because neither’s operations has to involve the other. Until, inevitably, they do, and the process of breaking down those walls can be extraordinary.
What Southern Devall needed was a unified digital platform—one built to streamline operations, reduce long-term costs and support the safe, efficient movement of chemicals along the Gulf Coast and Mississippi River. Kalypso was brought in to help realize that vision.
Bridging the Operational Divide
Southern Devall faced significant operational silos stemming from its history as two separate companies—Southern Towing Company and Devall Towing. In the combined organization, these divisions still primarily operate in their original respective domains (river and coastal transport), and their systems and processes remain fragmented. SD relied on a patchwork of purchased and homegrown software solutions for key functions such as maintenance, logistics and crewing, with some departments still managing critical processes manually. Without a unified system, SD struggled with inefficiencies, lack of visibility and limited access to data-driven insights.
Recognizing the need for an integrated digital solution, SD launched "Project Zulu" (which in nautical references means, “I require a tug”), aiming to consolidate its operations into a single, scalable platform with Rockwell Automation’s FactoryTalk® DataMosaix™. The goal was to enhance efficiency, improve decision-making and drive profitability by gaining real-time insights across its entire fleet and workforce.
First, we created a central hub for defining data models for Towboats, Barges, Terminals / Docks / Berths, Locks, Fleets, Waterways, Cargoes and Customers; each with detailed metrics such as a vessel’s length, air draft, number of engines and critical spares.
Then, we tackled logistics: Towboats picking up Barges, each “Trip” consisting of multiple “Voyages,” and a workflow for the logistics team to enter, track and update these orders. We added a notification system so the ship-side crew could receive, acknowledge and update their progress in real-time until a Barge had been delivered to a customer and the Trip was completed.
Next, we streamlined crew management with employee data already linked to SD’s ADP system. SD needed a better way to specify which employees were on which vessels, and when. And even if their “home” was permanently on a particular vessel, everybody has time off (“Off-Hitch”), and we need to know who is actively on the vessel at a particular time. So, we implemented a drag-and-drop tool that allowed easy and quick redefining of which ship-side employees were on which-vessels for assigning crew members to vessels, and accounting for shifts and time off.
We then digitized Coast Guard-mandated logs, replacing paper records with automated notifications and structured entry fields to ensure compliance. There are an extensive set of Coast-Guard-mandated/legally binding logs (the “Towing Vessel Record”) which had to be implemented. These requirements vary between the River and Coastal Divisions, and some logs are only entered occasionally, while others are mandated 4-times-per-day / every-6-hours-on-the-hour. We also built tools for the shore-side office for reporting incidents, tracking accidents and managing maintenance schedules – covering everything from engine checks to routine cleaning.
Beyond operations, we provided essential system-wide improvements, including SSO login, user role management and UI/UX enhancements for both function and aesthetics. SD now has an integrated platform that keeps SD’s fleet running smoothly while ensuring compliance, safety and efficiency.
Navigating Global Teams & Connectivity Constraints
With development teams in India and stakeholders in the U.S., time zone differences made real-time collaboration difficult. To stay aligned, the team implemented structured check-ins at the start and end of each development day, maintaining clear communication and accelerating decisions.
Connectivity on the water was another constraint. Most vessels rely on cellular networks, limiting real-time data transmission. While GPS tracking was successfully deployed, broader IoT integrations were scheduled for a later phase, once satellite connectivity could be established across the fleet.
A Phased Approach to Integration
Kalypso collaborated closely with SD stakeholders to design and implement a robust, centralized solution that lets Southern Devall manage every aspect of their operations, from tracking vessels and cargo to managing crew assignments and compliance.
The project structure contained three key phases:
Phase 1
Proof of Value & Requirements. Our team created mock-ups and demos to validate our capability in delivering a comprehensive solution. This phase established the foundation by aligning business requirements with technical feasibility.
Phase 2
Core Development & Implementation. With a structured waterfall approach, a larger development team—at times scaling up to twenty developers—worked to build the core system. Leveraging the FactoryTalk DataMosaix Private Cloud (DMPC) platform, the team accelerated development while ensuring seamless integration with SD’s operational workflows. This phase culminated in the near completion of all major functional requirements.
Phase 3
Agile Enhancements & Go-Live Readiness. Transitioning to an agile approach, this phase focused on refining the system based on real-world SME feedback. Our team worked in two-week sprints, addressing logistics refinements and high-priority items identified by SD’s new project lead. A pilot program involving two rivers and two coastal towboats were scheduled to coincide with the post-implementation support ensuring a smooth transition to full-scale deployment.
Enabling Visibility Efficiency & Data-Driven Decisions
Southern Devall has created a single, integrated platform that connects its fleet, crew and shore-side operations. The new system consolidates critical functions, streamlines day-to-day workflows and provides real-time visibility into assets, compliance status and operational performance.
“With the help from Kalypso, Southern Devall is well on its way to having one site where Captains receive their voyage orders, enter regulatory information from the vessel, track maintenance, and report incidents, live location of assets via GPS, and so much more,"
— said Carlin R. Chapman, Executive Vice President, HSSE & Compliance at Southern Devall.
Our work together has enabled —
- Full visibility into towboat locations, crew assignments and trip progress
- Reduced reliance on manual processes across logistics, crewing and reporting
- Improved compliance through digital Coast Guard logs and automated alerts
- Better data to support predictive maintenance and future AI-driven operational enhancements
- A more intuitive experience that shortens onboarding and increases adoption
With the pilot program in motion, Southern Devall is now leveraging its data to drive strategic decisions, reduce risk and operate with greater clarity and control.
Ready to transform your business's digital future?
Thought Leaders
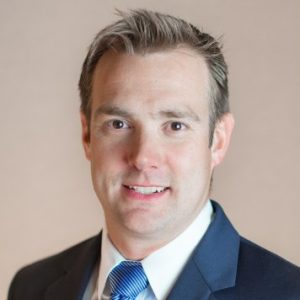