We trained the algorithm to predict bad splices before they happen and prescribe pressure setting adjustments to bring the splice within tolerance.
Kalypso employed a Gradient Boosted regression algorithm comprised of the target variable (splice length) and real independent variables (material cut length, previous splice length, etc.) as well as featured engineered independent variables (splice moving average, splice variance based on last rolling N tires, etc.) to first train a model to predict whether the next splice is likely to be out of tolerance.
When the machine learning algorithm predicts the splice will be out of tolerance, the pressure roller set parameters are directly adjusted to bring the splice within tolerance utilizing an interface to the machine control system.

A quick primer on how tires are made
Tires start out as rectangular pieces of rubber referred to as the tread which gets wrapped around a cylinder drum.

The point where the ends meet is called the splice which must fit within a given tolerance to be considered a “good” tire.

On top of the building drum there is a pressure roller which can be manipulated to adjust the final splice overlap.

The goal is to ensure the two ends are joined together within the tolerances for overlap to create a stable join.
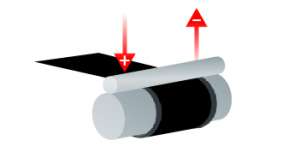
A too-short splice requires more pressure to be applied to lengthen the material, a too-long splice length requires less pressure.
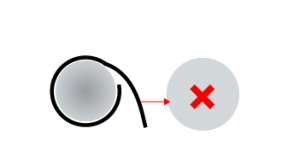
Too much or too little pressure can result in scrap or rework, contributing to downtime and fewer tires produced.
Our work made it possible to make over half a million more tires every year.
We exceeded our initial target achieving:
- 45% reduction in downtime
- 100+ more tires per machine per day
- 550,000 more tires per year