As part of their manufacturing process, the company operates multiple boilers for steam production. We helped improve how they monitor emissions from their boilers. Before our work together began, the company faced increasing challenges with their traditional hardware-based Continuous Emission Monitoring Systems (CEMS).
Hardware CEMS are expensive to operate, throughout their lifecycle they incur:
High Maintenance Costs — The hardware analyzers required significant upkeep, including regular calibration, part replacements and specialized maintenance personnel.
Monitor Downtime — Monitor downtime risked non-compliance with environmental regulations that mandate minimum uptime requirements of 95%.
Capital Expenditure — Replacing aging hardware CEMS would involve substantial capital investment, including the cost of new analyzers, shelters, heated sample lines and additional infrastructure.
The company needed a cost-effective, reliable and accurate solution to monitor emissions, ensure regulatory compliance and align with their sustainability goals. We were engaged to implement and validate a software-based continuous monitoring solution - Software CEM® - to address these challenges.
Our work resulted in 99% monitoring uptime and continuous years of passed Relative Accuracy Test Audits (RATAs), supporting their regulatory and operational goals and their brand promise of creating products sustainably.
We partnered with the Client to implement a Software Continuous Emission Monitoring System (Software CEM®)
Implementation began with a single boiler, where the Software CEM® was run concurrently with the hardware system to demonstrate accuracy and reliability. Upon successful validation, the solution was scaled to additional boilers across their facilities.
Our approach focused on sustainability and working within existing constraints, including leveraging existing equipment:
Accurate Emission Calculations — Developed predictive models by collecting and analyzing process data (e.g., fuel flow, air damper positions, temperatures) to accurately calculate emissions without direct measurement.
Leveraged Existing Infrastructure — Utilized existing process sensors and data historians already in place for boiler operation and safety, maximizing the value of current assets to feed into mathematical models.
Eliminated Physical Analyzers — Eliminated the need for expensive hardware analyzers and supporting infrastructure.
Rigorous testing and validation — Conducted rigorous testing and validation, including side-by-side comparisons with the existing hardware CEMS and passing the EPA's Relative Accuracy Test Audit (RATA), ensuring the software solution met all regulatory requirements.
Traditional Hardware-based Continuous Emission Monitoring Systems (CEMS) come with significant capital and environmental costs:
- Significant Capital Expenditure — Purchasing and installing physical analyzers, shelters, heated sample lines and calibration gases requires substantial investment.
- High Maintenance Costs — Continuous upkeep of hardware analyzers, including regular calibration, part replacements and specialized personnel, increases operational expenses.
- Operational and Regulatory Risk — Physical analyzers break down, especially in harsh industrial environments, leading to increased monitor downtime and potential non-compliance with regulations that mandate minimum uptime requirements.
- Increased Carbon Footprint — The operation of hardware analyzers and associated equipment consumes additional energy and resources.
- Scaling Limitations — Scaling hardware-based CEMS leads to exponentially increasing costs, as physical equipment constraints prevent economies of scale.
Our work enabled continuous emissions monitoring while minimizing downtime, reducing costs, and protecting brand reputation
Our solution delivered immediate value through substantial cost savings on hardware and maintenance, while achieving industry-leading 99% monitoring uptime. The implementation provides rich operational data insights and is easily scaled across multiple facilities, establishing a new standard for emissions monitoring in the sector.
Thought Leader
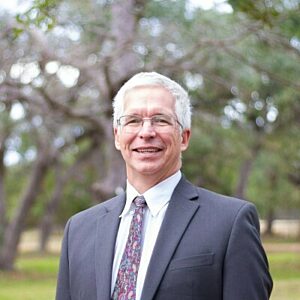